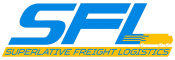
About Superlative Freight Logistics
Superlative Freight Logistics (SFL) provides comprehensive freight and logistics services, helping companies efficiently manage their supply chains. SFL approached us with the need for a custom Warehouse Management System (WMS) to streamline their warehouse operations. Their existing process involved a large spreadsheet that tracked pallet scanning and inventory management, but it had become inefficient as the data grew in volume. They needed a solution to replace this cumbersome system, providing better performance and scalability.
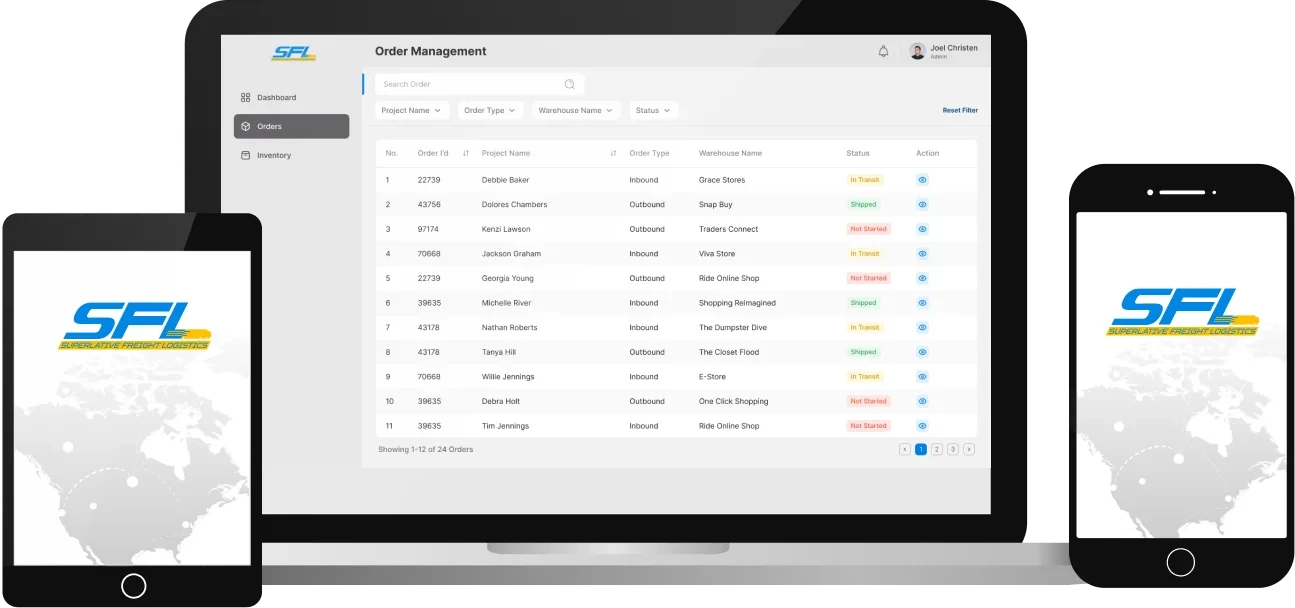
The Challenge
SFL was managing warehouse operations using a comprehensive spreadsheet that was slowing down due to the large amount of data being processed. They needed a scalable Warehouse Management System to improve inventory tracking, optimize warehouse performance, and provide visibility to their customers—EPC Companies, Asset Management Companies, and Manufacturers. The new system had to support SFL Admins, Warehouse Associates, and Customers, offering a robust feature set for managing inventory, scanning pallets, and tracking warehouse activities.
Our Strategy
Our team approached this project systematically, breaking it down into distinct phases:
Phase 1
Discovery
We began by identifying the limitations of the current spreadsheet-based system and outlining the key features required for the Warehouse Management System. This phase helped us understand the needs of SFL Admins, Warehouse Associates, and Customers.
Phase 2
Planning
In collaboration with SFL, we established the high-level framework of the WMS, setting clear acceptance criteria and outlining the architecture for a platform that would support mobile, tablet, desktop, and web interfaces.
Phase 3
Design
Our UI/UX team designed an intuitive, easy-to-use interface that meets the needs of different users—Admins, Associates, and Customers. We prioritized a responsive layout to ensure compatibility across all devices, focusing on simplifying workflows for each user type.
Phase 4
Development
Our development team worked on creating a feature-rich Warehouse Management System with robust inventory tracking and scanning functionalities. The backend was built to efficiently manage large volumes of data, while the front-end was designed to be intuitive and responsive. Special attention was given to integrating warehouse-specific scanning devices for seamless operations.
Phase 5
Testing & Security
We conducted comprehensive testing to ensure data accuracy and system stability. Our QA engineers verified every functionality, from inventory updates and scanning to reporting, ensuring the WMS met the highest standards of performance and security.
Phase 6
Launch & Maintenance
After a successful launch, we continue to provide ongoing support to ensure the WMS operates smoothly and remains aligned with SFL’s evolving needs. Feedback from warehouse staff and customers is continuously incorporated to improve the system.
Phase 1
Discovery
We began by identifying the limitations of the current spreadsheet-based system and outlining the key features required for the Warehouse Management System. This phase helped us understand the needs of SFL Admins, Warehouse Associates, and Customers.
Phase 2
Planning
In collaboration with SFL, we established the high-level framework of the WMS, setting clear acceptance criteria and outlining the architecture for a platform that would support mobile, tablet, desktop, and web interfaces.
Phase 3
Design
Our UI/UX team designed an intuitive, easy-to-use interface that meets the needs of different users—Admins, Associates, and Customers. We prioritized a responsive layout to ensure compatibility across all devices, focusing on simplifying workflows for each user type.
Phase 4
Development
Our development team worked on creating a feature-rich Warehouse Management System with robust inventory tracking and scanning functionalities. The backend was built to efficiently manage large volumes of data, while the front-end was designed to be intuitive and responsive. Special attention was given to integrating warehouse-specific scanning devices for seamless operations.
Phase 5
Testing & Security
We conducted comprehensive testing to ensure data accuracy and system stability. Our QA engineers verified every functionality, from inventory updates and scanning to reporting, ensuring the WMS met the highest standards of performance and security.
Phase 6
Launch & Maintenance
After a successful launch, we continue to provide ongoing support to ensure the WMS operates smoothly and remains aligned with SFL’s evolving needs. Feedback from warehouse staff and customers is continuously incorporated to improve the system.
The Solution
We built a custom Warehouse Management System for Superlative Freight Logistics that provides comprehensive inventory management across multiple warehouse locations. The solution allows SFL Admins to manage customers, track orders, and oversee inventory operations effectively. Warehouse Associates can scan pallets using Zebra Android devices and through the app, with real-time updates to the system, ensuring seamless inventory tracking. Customers can also log in to view reports, track orders, and access inventory details.
The platform is designed for scalability and ease of use, providing SFL with the ability to manage large volumes of inventory data without the slowdowns that had plagued their previous spreadsheet solution. The integration of advanced scanning capabilities and analytics tools further enhances operational efficiency and customer satisfaction.
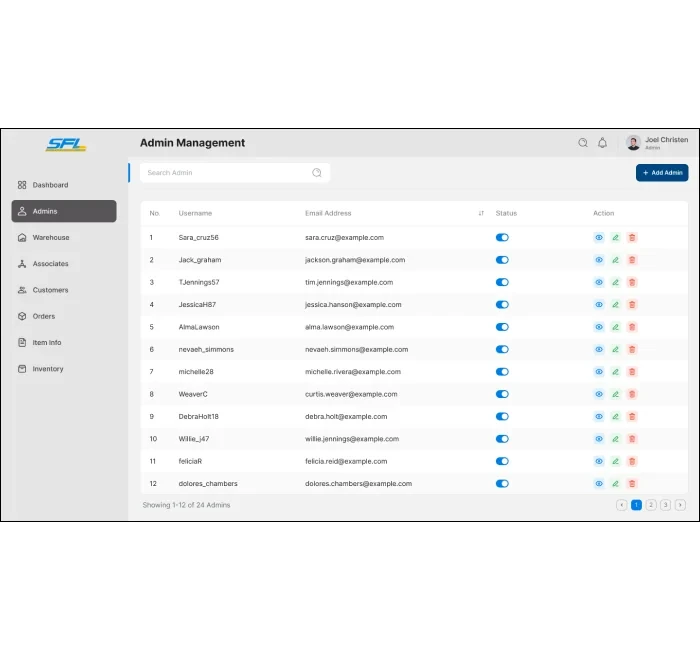
The Results
The implementation of the Warehouse Management System has significantly improved SFL’s warehouse operations. By replacing the outdated spreadsheet solution, we have provided SFL with a scalable, reliable, and efficient way to manage inventory, track orders, and oversee warehouse activities. The new system has led to quicker processing times, reduced errors in inventory management, and improved transparency for SFL's customers. Superlative Freight Logistics now has the tools they need to efficiently manage their operations and provide a better experience for their customers.